Fall 2022
Building Resilience in Supply Chains
– Stephanie Bowen
A primer on supply chain resiliency with Yossi Sheffi, PhD, director of MIT’s Center for Transportation Logistics.
When we decided to dedicate our fall 2022 issue to the complex issue of global supply chains, we knew we needed to look forward to advance the conversation that has been taking place since the COVID-19 pandemic laid bare serious weaknesses previously unnoticed by many. As this issue’s articles, essays, and features started taking shape, it also became clear that we needed to take a step back. That’s when I reached out to Yossi Sheffi at MIT. Who better to help us establish the principles of a resilient supply chain—past and future—than the person who has studied and written about the topic for decades, and who is helping to prepare the next generation of supply chain professionals?
Our conversation has been edited for clarity:
Stephanie Bowen: Tell me a little bit about yourself and your work at MIT.
Yossi Sheffi: I’m a professor of engineering systems at MIT and the director of MIT’s Center for Transportation Logistics. It’s an interdepartmental center, which means it has people from all departments working on research programs. There are about 100 permanent staff and close to 100 graduate students, but the faculty members associated with departments come and go depending on research under way.
SB: What are the goals of the program?
Some companies drill and prepare all the time. Companies need to have an emergency management center where all the information is centralized and decisions can be made quickly. Companies also have to decide who makes the decisions.
YS: We are trying to develop sophisticated and innovative methods to make more resilient supply chains. In particular, we work with industry in order for these innovations to be implemented. As part of this, we have a group of 50 companies that are working with us very closely in what we call “the supply chain exchange.” We have multiple activities with them, including roundtables and conferences, both online and in-person gatherings, both at MIT and at members’ locations. For example, tomorrow, our members are going to Wayfair to look at its logistics and how it manages its supply chains. Topics for a gathering like this are usually suggested by the members. Importantly, the companies also work with our students.
SB: Can you talk more about MIT’s supply chain research?
YS: The areas of research range from resilience to network optimization, humanitarian logistics, freight transportation, food supplies, inventory management, last-mile delivery, and so on—we have many, many subjects. We oversee about $15 to $20 million worth of research grants a year, mostly from industry but also from governments.
SB: Supply chains have been very important for a long time, but it seems the world did not fully understand their significance until the COVID-19 pandemic. Can you talk about shifts in understanding?
YS: In 2001, after 9/11, I was in the UK working with people from some of the bigger British companies. One of the politicians asked, “What happens if the next Al-Qaeda attack is not on a symbolic target but on an economic target like a port or a refinery?” Most of the assets in the UK and the US are owned by private companies, so he asked what the companies were doing. People looked around the table and said, “Nobody knows.” For me, this was a wake-up call to the need to build resilience in supply chains. My first business book came out in 2005, and I wrote even then that there are not enough medical ventilators in the United States, as an example of the country not being prepared. And companies were not prepared. A few companies like Intel were thinking about it all the time and getting prepared, but most companies were not.
So, some of us were screaming from the rooftop for a long time that the country is not resilient. We were not arguing for what people are arguing now—for getting out of China, for example, or building mountains of inventory. Interestingly, only during the recent pandemic did people start calling me from CNN and Bloomberg and the Wilson Center and all kind of places.
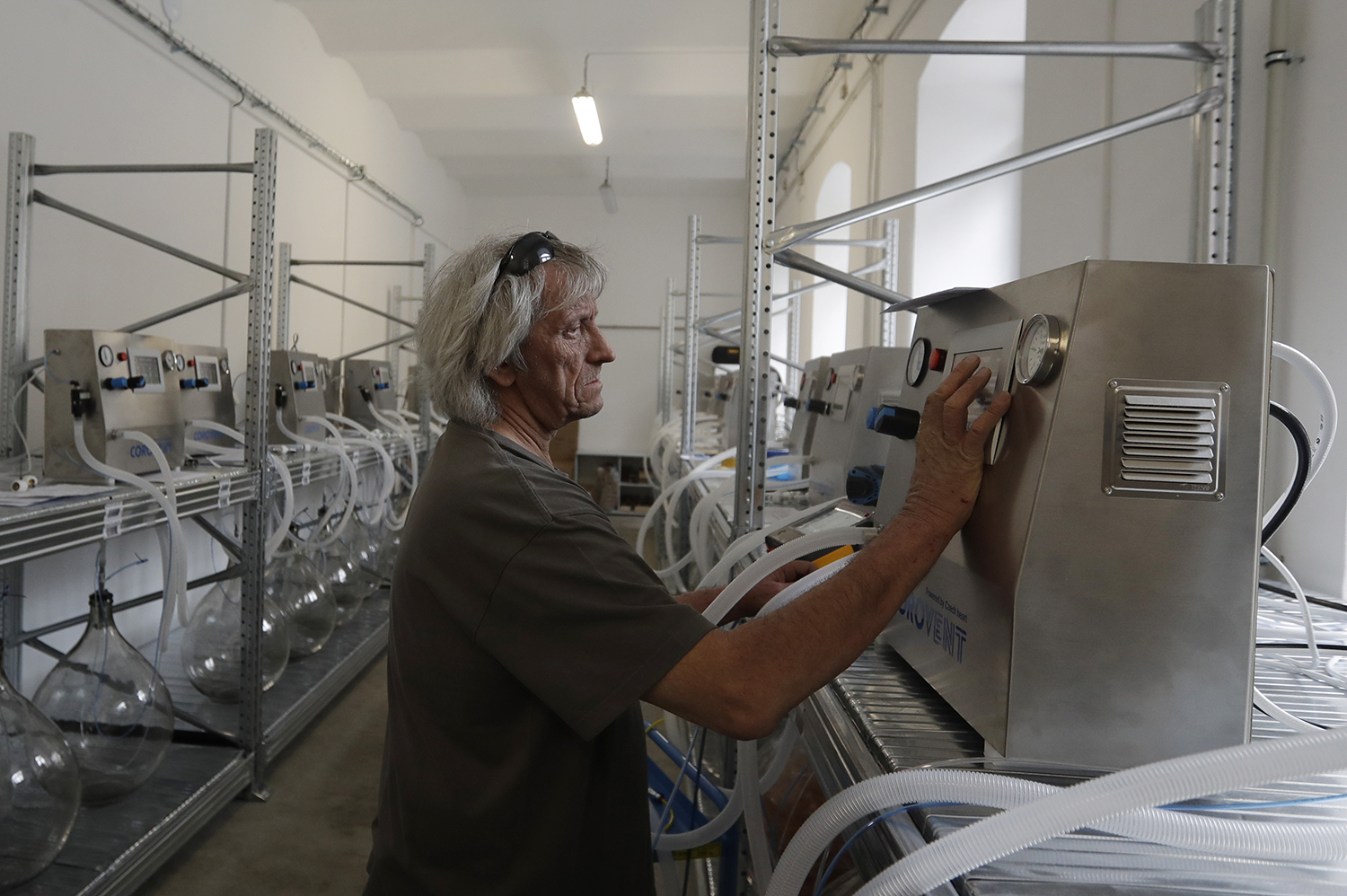
SB: I remember news story after news story about supply shortages, empty shelves—it was as if nobody had heard of a supply chain before. What did the media get right? What did they get wrong?
YS: The media is slowly getting better. But even the New York Times admitted that before the pandemic, it didn’t have a beat on logistical supply chains. I cannot tell you how many calls I got during the height of shortages. I was getting calls from reporters that sounded like this: “Professor Sheffi, I am working for—whatever place they were calling from—and it went like this, ‘Until last week, I was a sports reporter. They asked me to write about supply chains. What can you tell me about supply chains?’” Just like that. They didn’t have any expertise on this. Do you remember headlines about running out of food, running out of eggs, running out of meat because plants were closed? The US is the fourth-largest exporter of meat in the world. We have more meat than we know what to do with. So there was never really any shortage, even when a few plants were closed for a short time. Now, people are catching up, of course.
We have low-cost sensors that can be put into shipments to tell you exactly what happens to the shipment along the way. It transmits the location continuously. It tells you if the doors of the containers are open, if the temperature goes up.
SB: When you were shouting on the rooftop that “We're not prepared,” were there specific things other than ventilators that you were shouting about, or was it just generally that we were not prepared and we must be? How has the conversation shifted?
YS: The example of the ventilator was not common for me because it was a government example. Most of my work is with companies. I was talking to companies about how to bolster their resilience, how to be able to respond, how to create the ability to be agile and quick and go from one supplier to another. I did not argue for having large amounts of inventory because companies that do that would not be competitive. I did not argue about getting out of China or reshoring because companies that would do that would not be competitive. The trick is to be competitive and to be resilient. And a lot of it is preparation. We can go through a whole list of how do you prepare, how do you create, how do you drill. Good companies drill all the time.
SB: Let’s do that—how do you prepare? What does a supply chain drill look like?
YS: Let’s take Cisco, which at the time had 18 playbooks for all types of disruptions. What do you do? Who is responsible? How do we manage it? Today, Intel goes to its plants all over the world and tells the plant manager, “You know about this supplier of critical material? They’re now out of business. What will you do?” And they have to find another supplier—and then get a new contract with a transportation carrier, and move it through different ports.
Some companies drill and prepare all the time. Companies need to have an emergency management center where all the information is centralized and decisions can be made quickly. Companies also have to decide who makes the decisions. There are many examples of people who, by making a quick decision, were botching the flows in the system—some warehouses had too much stuff, and others were empty.
During the pandemic, General Mills reduced the number of Progresso soups from 90 varieties to 50 varieties. Why? So that they could make sure that the stuff that most people like is on the shelf. And it cut change-over costs.
You also need a communication process because Wall Street and customers and the community and suppliers are all worried. If you don’t communicate obsessively, they’ll assume the worst.
During the pandemic, Korean Airlines was the only airline that made money. On a dime, it shifted its airplanes from passenger service to freight.
SB: One of MIT’s goals is to bring innovations to supply chains. What are some of the most exciting innovations on the horizon?
YS: We have low-cost sensors that can be put into shipments to tell you exactly what happens to the shipment along the way. It transmits the location continuously. It tells you if the doors of the containers are open, if the temperature goes up. You know if something goes wrong, which means you can react—you can do something about it—before the container or the trailer comes to your warehouse or store. Strategically, if you know exactly what’s going on and when your shipment will arrive, you will know exactly how much stock you will need until the next replenishment.
Many, many efforts are going toward increasing what’s called visibility. It is still limited, because what you really want to know is not only what takes place during shipping but also what’s going on at your supplier’s plant. And you want to know their limits. You can do this now, but only to a limited extent.
Something that started before the pandemic is new software applications to find out the implications of something going wrong at one of the suppliers. I’ll give you an example. You find out that Northern Italy closed because of the pandemic. This software will immediately tell you which of your suppliers or plants are in the area, what parts they are making, which products these parts go into, and which customers are getting this product. This means that within seconds, once you understand that Italy is closed, you will know how much of your revenue is at risk and what to do about it. These are all steps designed to mitigate the consequences of disruptions.
We cannot have one-issue policies. We cannot have a green policy or a mining policy. We need to have balanced policies that look at both benefits and costs, and look at them over time.
After Hurricane Katrina, there was a lot more work coordination between government and the private sector. FEMA started realizing that if Walmart has a distribution center that has water in the affected area, they don’t need to send water there. Every state now has a joint public-private emergency management center. So Massachusetts has one, Boston has one, and so do many other states and cities.
There’s also a lot of new software to help you understand what is going on inside a company. If you’ve never worked in a company’s supply chain, you’d think it was ridiculous. But there’s a need to find one version of the truth. Because in many companies, the salespeople, the procurement people, the finance people, and the manufacturing people all have their own forecasts, their own metrics, their own findings. But it’s important to be able to get just one version of the truth—the most likely version—and then work from it.
During the pandemic, many companies actually improved their processes because it was an existential threat and responses to the situation had to be implemented quickly. Of course, some companies were better at this than others.
For example, during the pandemic, Korean Airlines was the only airline that made money. On a dime, it shifted its airplanes from passenger service to freight. It removed seats and started hauling freight. A lot of other airlines hesitated, and didn’t do it. Why was Korean Airlines successful? It was agile. It was the only airline that was, and it made the most money. So there are examples of companies that were flexible—making quick decisions and mitigating the impact of a disruption as big as the pandemic.
There’s also a lot more automation that’s coming, in part because people are saying “Well, the robots don’t get sick.” And also in part because, to an extent, robots are relatively inexpensive. And, over time, they will be even cheaper. Everything with electronics, with AI—artificial intelligence—is becoming less and less expensive over time; people are not.
SB: Let’s shift a bit, from business to policy. One of the biggest AHA moments during the pandemic was seeing those long lines of cargo ships full of shipping containers full of products waiting to get off the dock at the Port of Los Angeles. In reaction to either that moment or the culmination of moments like that, what did policymakers get right? What did they get wrong?
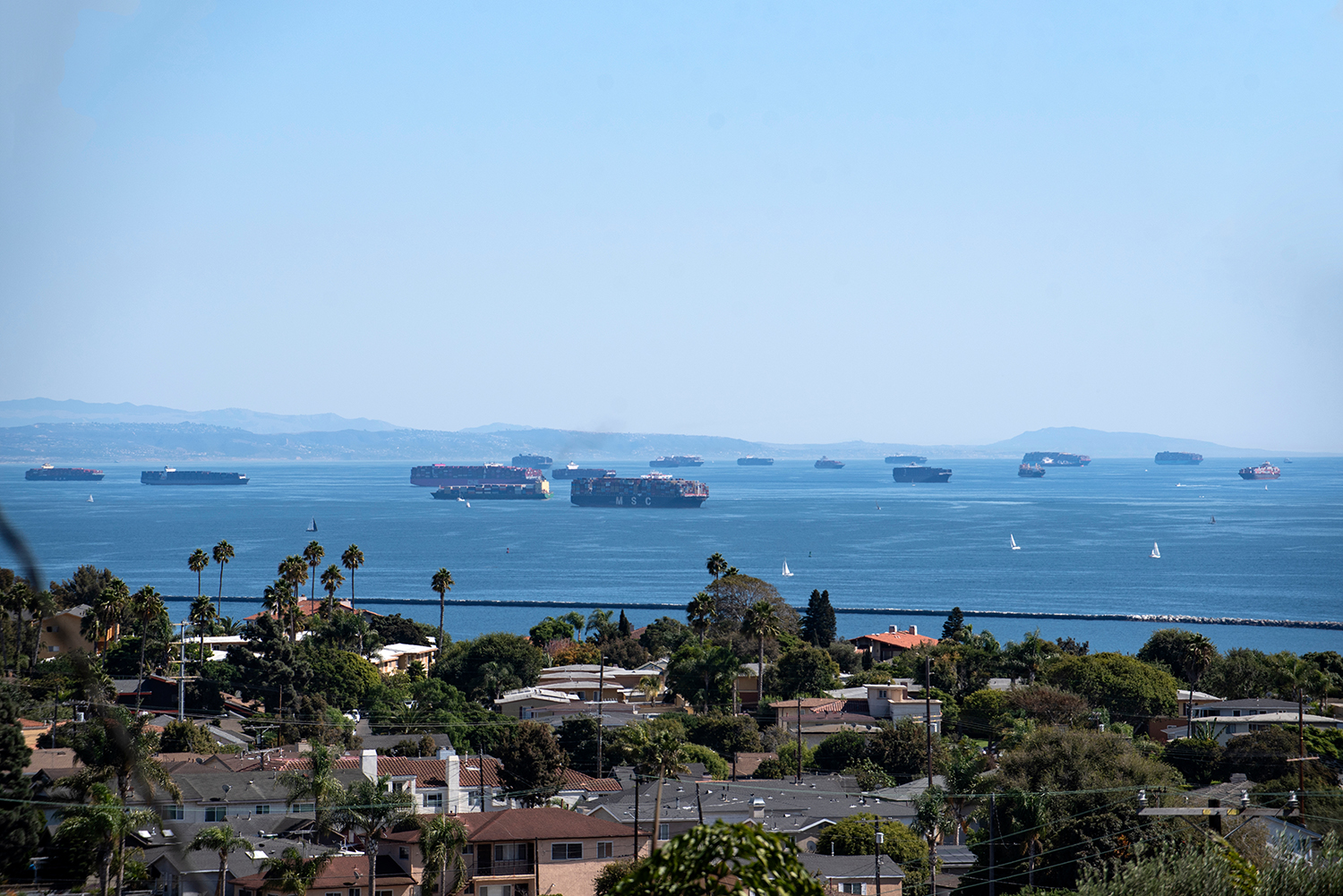
YS: The government’s absolute mistake was showering people with money indiscriminately. It’s a mistake that will live with us for long time. It’s a mistake that created the current inflation. It’s a mistake that created the current shortages. If you just give people money, they’ll buy. Supply is physics. There is only so much capacity, so many ships, so many trucks. Plants can work only so much.
Sure, there are other factors. China closing here and there, and the fact that, honestly, the US ports are third-world ports compared with Singapore, Rotterdam, or Dubai. But this is not the issue because Rotterdam also has a line of ships waiting there and because even Rotterdam, one of the best ports in world, doesn't have unlimited capacity.
I will give you a forecast that you can take to the bank: Two or three years from now, or even sooner, there will be a lot of chips, all kind of chips. It takes three or four years to build a fabrication plant for chips. It doesn’t happen overnight. So the US, the EU, South Korea, and Japan are all investing in building chip plants. Many of the leading chip companies will not be able to sell the new chips at current prices. And of course, they know it. They will build plants in the US, EU, and elsewhere, but only with government support.
SB: Are there one or two things that will really help create supply chain resilience that you would recommend to policymakers?
YS: OK, this will sound awful. The whole idea of going right now to a greener world is a mistake. It’s not that I don’t believe in global warming. But at this point, the green policy ideas of not allowing pipelines, not allowing drilling on federal land, limiting gas exports, and all this need to be examined. Implementing these ideas gets Europe on the back foot when trying to help Ukraine and makes us go hat-in-hand to Saudi Arabia begging for more oil production.
You want to increase the price of carbon-based fuel? Great. That makes renewables more appealing. But renewables are limited. As long as we depend on wind, as long as we depend on solar, as long as we depend on water in all the drought-prone areas, it’s limited. You’re going to get only that much.
We cannot have one-issue policies. We cannot have a green policy or a mining policy. We need to have balanced policies that look at both benefits and costs, and look at them over time. So, yes, we all want renewable energy. We all worry about global warming. But I’m more worried right now about Russia and Ukraine. I’m more worried right now about whether China is going to attack Taiwan.
Stephanie Bowen is the editor of the Wilson Quarterly.
Cover photo: Korean Air cargo plane at airport. Air freight and shipping. Aviation and aircraft. Transport industry. Global international transportation. Fly and flying. Copyright (c) 2022 Soos Jozsef/Shutterstock.